
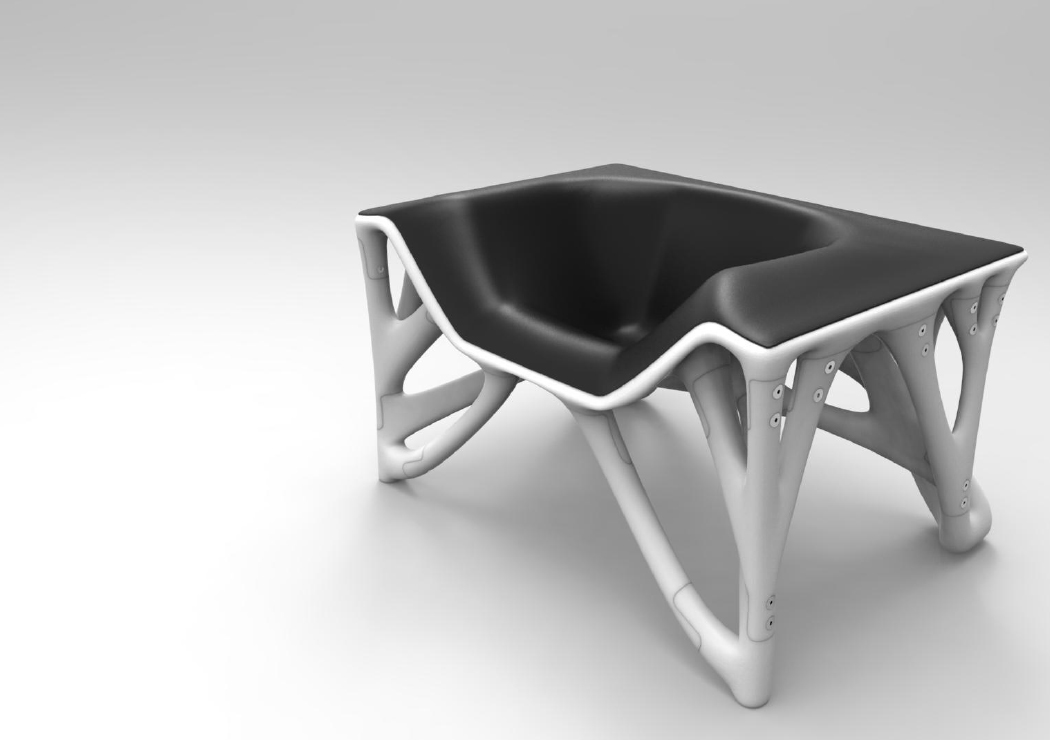
- #Solidthinking inspire student how to#
- #Solidthinking inspire student license#
- #Solidthinking inspire student plus#
Project 5 – Wearable Devices (With BlocksCAD)įind many more lessons in the Apps for Kids Classroom learning environment.
#Solidthinking inspire student how to#
and I think that's amazing and inspirational.” - Sydney, Age 12 Educator ResourcesĬheck out the sample lesson plans below to learn how to run your own fun class projects! "This program shows great opportunity for … learning about how things work.

#Solidthinking inspire student plus#
#Solidthinking inspire student license#
I only need one license for one computer.Engineers can set up their simulation in five easy steps: Inspire Case provides a fast, easy, accurate, and affordable framework for engineers to determine casting feasibility early in the development process. Reduce costs: By removing the need for so many physical prototypes, organizations save on material usage and design time.Accelerate the design process: By simulating early, teams can determine which aspects of the design need to be re-evaluated removing unnecessary and time-consuming redesigns or reiterations.What’s more, they can assess static loads, normal modes, buckling, and motion to ensure quality and dependability before building a physical prototype. Explore design concepts: Simulation allows designers and engineers to explore more design concepts without additional prototyping costs.This helps organizations meet their critical goals including increasingly quality, decreasing costs, and speeding up time to market. Simulation is no longer the last step in the design process, in order to stay competitive in the market, simulation must be completed early and often in the design process. Improved profile editor: Have more control over profile parameters and preview the built-in actuator and motor profiles.Spot welds: Engineers can now apply spot welds at any location on a surface part of any other existing point.Friction for rigid joints: You can now analyze forces caused by friction during motion analysis with the ability to specify joint type and friction levels.Plus, you can now also use the Load Cases table to import and export for a. Import/export load cases/tables: This functionality has been redesigned so you can more easily view all loads and select the specific cases that you want to apply them to.PolyNURBS update: Easily create complete CAD and manufacturing-ready geometries post-simulation using the PolyNURBS Fit tool and then automatically fit it to an optimized shape.Overhang shape controls: When designing for additive manufacturing, eliminate overhangs to create a more self-supporting structure.Lattice optimization, visualization, and export: Automatically generate optimized lattice as well as mixed solid-lattice structures.
